White Paper: Understanding the Benefits of 10, 25, 50, and 100GigE Vision
Ultra-high data and frame rates, low CPU overhead, cable length options, affordability, and simplicity are among many GigE Vision advantages.
With demand for high-speed solutions driving machine vision applications, manufacturers have many choices when it comes to components. Frame grabbers are one option. However, by making changes at the driver level — alongside existing high-speed network card technologies — it is possible to achieve 100GigE speeds and beyond with equal performance and lower costs than frame grabber–based technologies. The following presents a brief timeline of GigE Vision cameras; details, advantages, and benefits of the interface; and information on using 10GigE up to 100GigE to stay on the leading edge of machine vision solutions in manufacturing and beyond.
A Brief Background on GigE Camera Evolution
In 2010, Emergent Vision Technologies introduced the first camera with a 10GigE interface. Advancing image sensors and demand for a higher-speed interface led tothe release of the first 25GigE cameras in 2018. Continuously increasing sensor speeds again drove high-speed vision demands, leading to 100GigE cameras in 2020 (Figure 1).
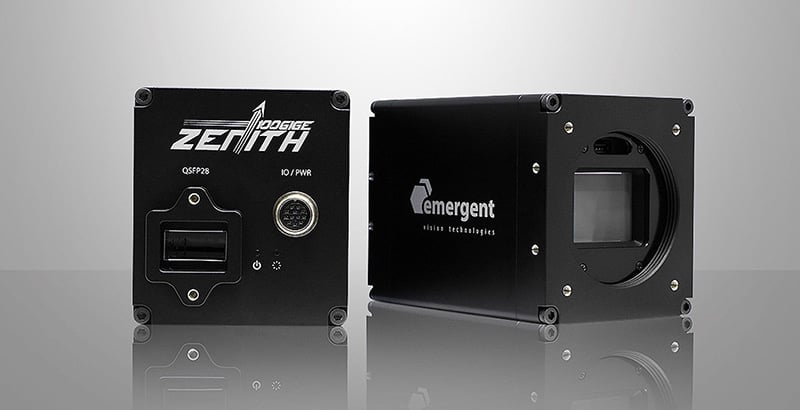
Today many GigE Vision solutions and accessories are available. Generally, cameras govern resolution and frame rate, which are defining factors in high-speed imaging applications. However, accessories and integration also play important roles in the image acquisition framework. A reputable machine vision technology company provides a complete acquisition solution and gives advice on well-tested architecture to deliver the performance necessary for ultra-high-speed applications.
Conventional to Optimized GigE
The conventional GigE frame acquisition model is presented in Figure 2. When 1 GigE is not optimal, Intel PRO/1000-based network interface cards (NICs) are preferred for higher-performance driver implementation.
The optimized GigE model shown in Figure 3 offers remote direct memory access (RDMA) and RDMA over converged Ethernet (RoCE). This system delivers low CPU usage and no missed frames, with low jitter and latency identical to CoaXPress (CXP).
The RDMA-optimized GigE model provides direct access from the memory of one host (storage or computer) to the memory of another host without involving the remote operating system and CPU. RoCE is the standard protocol that enables RDMA’s efficient data transfer over Ethernet networks, allowing transport offload with hardware RDMA engine implementation. This design network optimizes performance, with lower latency, lower CPU load, and higher bandwidth.
The GigE Vision Advantage
With IEEE standardization and the success of GigE solutions, manufacturers have many options for hardware, soft ware, and accessories. For example, a GigE Vision solution can use an off -the-shelf NIC or FPGA card to directly connect to a 100GigE camera, which reduces system complexity.
A driver in imaging system design is the demand for more advanced machine vision. Graphic processing units (GPUs) have seen increased use in applications involving higher speeds, 3D imaging, and deep learning, for example. Integrating a GPU can introduce AI solutions to drive advanced imaging systems. A major advancement in AI processing technologies is NVIDIA’s BlueField-2, which combines a NIC and GPU into a one-card solution. Such innovations continue to evolve and expand the capabilities of machine vision and imaging technologies.
With third-party off-the-shelf accessories, GPU support, fast data transfer, and increasing frame rates; the benefits of GigE cameras are expanding use outside the factory. As shown in Figure 4, two 25 GigE cameras with a dual NIC and a NVIDIA Xavier GPU deliver the precise architecture for drone system deployment.
As imaging solutions move out of the factory, GigE Vision’s ability to reduce complexity is increasingly important to OEMs. Furthermore, with SFP+ (10G), SFP28 (25G), and QSFP28 (100G) offering low-cost commodity transceiver parts, a single mode fiber can run up to 10 km and beyond. Cable length proves critical in applications where the camera may need to be far from the PC, such as surveillance, transportation, and sports technology. In brief, benefits to adopting GigE cameras include:
• Ultra-high data and frame rates
• Accessories and cabling options to cover long distances
• Camera synchronization with PTP (precision time protocol)
• Camera multiplexing and multicasting
• Low CPU overhead, low latency, and low jitter
• Strong cross-industry acceptance due to IEEE standardization
• Competitive cost and performance
Real-Life Examples and Comparisons: GigE Vision versus CoaXPress
The GigE Vision solution in Figure 5 shows 24 10GigE cameras, a switch for PTP synchronization, multiplexing the 24 cameras onto dual 100G links, and a single-slot 100G dual NIC for placing the image frames in system memory. The equivalent CXP system requires three octal frame grabbers. The differences between 10GigE and CXP6 in this example are shown in Table 1.
Another real-world deployment in Figure 6 shows 12 25GigE cameras, a switch, and a dual 100G NIC. For a CXP system to achieve the same level of performance as this setup, it would require 12 CXP12 cameras plus three separate CXP12 frame grabbers. Those looking to deploy a fiber CXP option for longer distances would also need to add six fiber adapters into the bill of materials, further increasing the total cost of the project.
In another example in Figure 7, it would require 2 CXP12 cameras – each with 8 ports – along with 4 CXP-12 frame grabbers to equal a GigE Vision setup comprised of two 100GigE cameras connected to a dual 100G NIC, further highlighting the cost efficiency of GigE Vision.
When working with multiple cameras, precision ti ming and ti me stamps help imaging systems execute scheduled and synchronized simultaneous acquisitions based on an internal ti me-based command, without needing an external trigger. Combining many images and data into a single stream requires computing and processing power. GigE cameras and accessories combine multiple cameras into an accurate stream in real time. The availability of affordable Ethernet switches gives system designers a simple way to enable IEEE1588 PTP for multi -camera synchronization to 1 us.
Having triggering options helps integration and helps expand GigE camera applications. For example, in the rare case that a customer wants to trigger cameras from the NIC, Emergent has its own dual-port 25Gb NICs and single-port 100Gb NICs with a front panel trigger port. Additionally, the FPGA card previously mentioned also has IO port functionality.
Software Eases GigE Integration and Operation
With GigE widely adopted in industry, there are many software options to consider. One example is eCapture free viewer software, which controls all camera functions for preview, capture, and save. Advanced functions include area of interest (AOI), integration control, and standard pre-processing, including brightness, gamma, and frame rate control.
The eSDK software development kit allows end users, systems integrators, and OEMs to integrate their Emergent Vision Technologies cameras into their own software and equipment if needed.
Emergent also offers eCapture Pro which is a full turnkey software for various applications such as AOI and volumetric capture for customers with limited development resources or no expertise in ultra-high-speed vision technologies.
High-Speed Imaging Interface of the Future
Advancements in imaging speed are largely driven by the emergence of new image sensors, which in turn are driven by high-speed application requirements. Many applications require high-resolution images, and without the fastest interfaces, frame rates may not meet requirements. Interfaces like 10GigE, 25GigE, 50GigE, and 100GigE meet the high-resolution, high-speed needs of applications such as virtual reality, volumetric capture, sports analytics, and automated optical inspection.
Additional GigE Vision benefits include low server utilization, simplified system architecture, multicast video technology, competitive cost and performance, and shorter time to market. These advantages have allowed GigE Vision solutions to expand imaging applications across several industries and will continue to do so.
A Clear-Cut Choice for High-Speed Imaging
When considering the benefits of GigE Vision for high-speed imaging, one might wonder if there were sufficient benefits for launching a new standard like CXP when GigE Vision cameras clearly offer the best choice for high-speed interface for machine vision applications. Considerations include:
• Ultra-high data/frame rates capable of 10G, 25G, 50G, 100G, and higher
• The same CPU and memory utilization using standard built-in NIC functionality
• Stable image acquisition timing
• Image acquisition does not slow down processing
• With small adjustments and off-the-shelf components, GigE can do virtually anything CXP can
• Power over cable disappears with CoaXPress over Fiber
• CoaXPress uses a multi-coax cable for high-speed, could use an extra cable for Ethernet power
• CoaXPress over Fiber uses the Ethernet physical layer
• CoaXPress over Fiber was an extension of CXP that attempted to bring it up to speed with GigE. (Think ultra-high-speed and long cable lengths)
• CoaXPress over Fiber only has a few camera vendors advising the standard
• The name CoaXPress itself refers to coaxial cable – which is not fiber – so the naming itself is misleading
• Faster time to market with GigE, since 10GigE, 25GigE and 100GigE are available NOW